Esta urbanización modular e insular se enfrentaba a un "mar de retos
Pregunta: ¿Puede utilizarse la construcción modular para construir una serie de edificios de viviendas asequibles y singulares, todos ellos con el aspecto de haber sido construidos en 1845, en una isla destinada a los ricos? La respuesta es, por supuesto, sí, pero la historia del equipo de Signature Building Systems y KOH Architecture es bastante interesante.
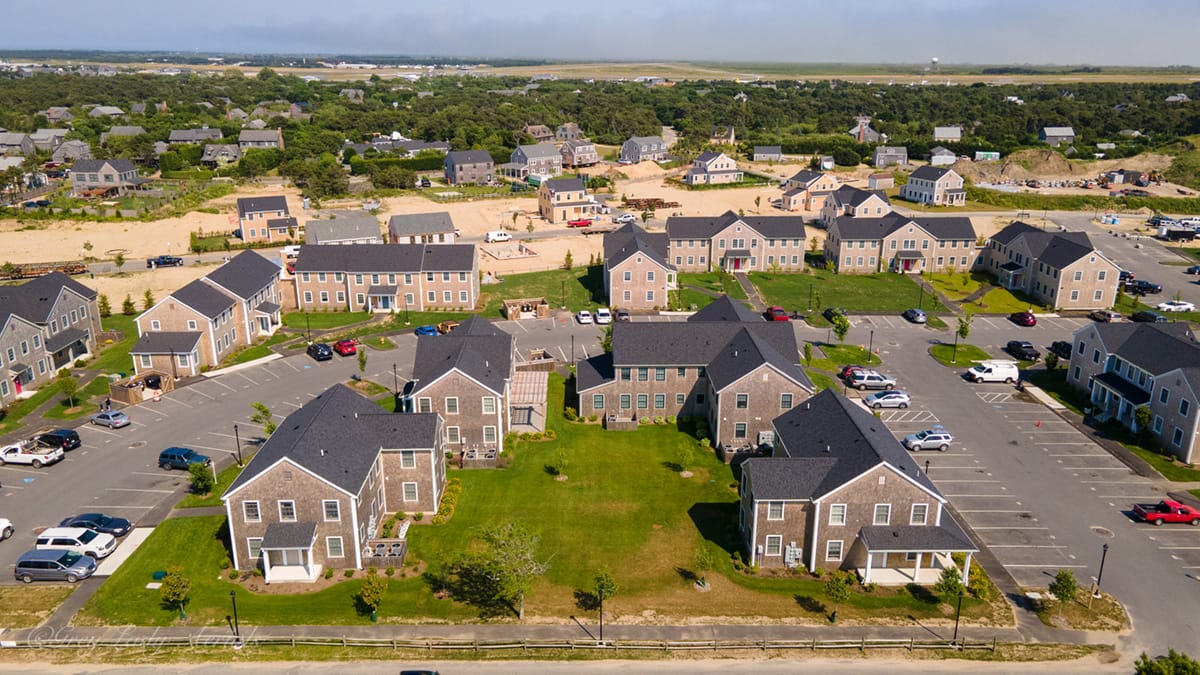
Esta urbanización de Nantucket, construida por Signature Building Systems y diseñada por KOH Architecture, constaba de 44 edificios y 455 módulos. Cada módulo tuvo que transportarse a la isla en barcaza.
La isla de Nantucket, frente a las costas de Massachusetts, es el hogar de algunos de los propietarios más ricos de Estados Unidos. Con una población de unos 17.000 habitantes, alberga todas las comodidades del continente, incluidos restaurantes, hoteles y Starbucks. De lo que carece, sin embargo, es de viviendas asequibles para quienes trabajan en estos negocios. La mayoría de los empleados viven en el continente y cogen el ferry para ir a trabajar todos los días, o viven en apartamentos en sótanos. Aunque en el pasado se ha intentado construir viviendas para los trabajadores de la isla, no hay suficientes para todos.
En 2017, Tom O'Hara, director de Grandes Proyectos de Signature Building Systems (SBS), se reunió con el promotor Phil Pastan, de Richmond Company Co. de Wilmington (Massachusetts). Pastan había adquirido 72 acres de terreno en el centro de Nantucket que quería convertir en viviendas asequibles para trabajadores y viviendas unifamiliares. El problema era que todos los edificios de la isla tienen que parecer construidos en 1845 y deben pasar por la Comisión del Distrito Histórico (HDC) antes de que se concedan los permisos de construcción. Si a esto añadimos que la mayor parte de la mano de obra de la isla está ocupada construyendo casas a medida, la conclusión natural era recurrir a la construcción modular.
O'Hara y su equipo convencieron a Pastan y a la arquitecta Dinah Klamert, de KOH Architecture, de que ellos eran el fabricante adecuado. Entonces empezó la diversión.
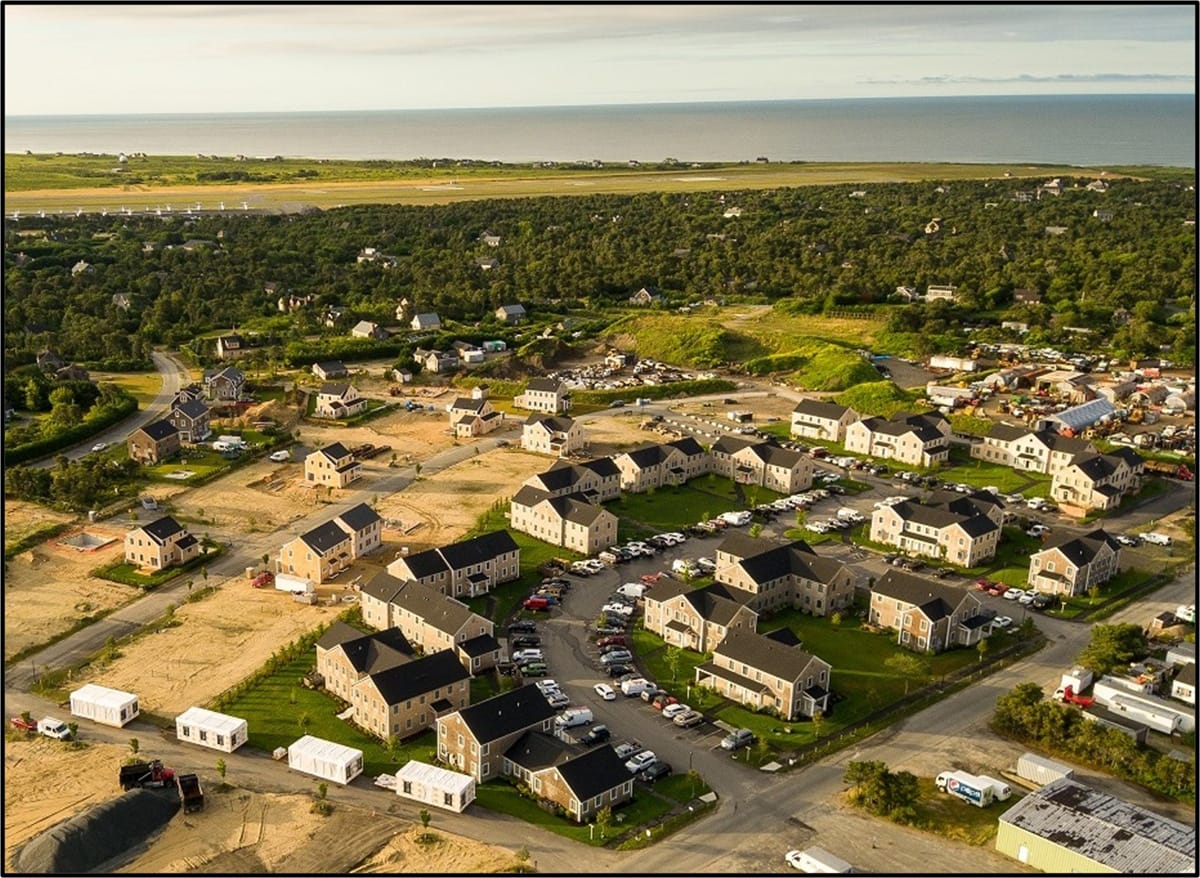
Un mar de desafíos
El proyecto se enfrentó a una serie de retos desde el principio: los requisitos históricos, la falta de mano de obra en la isla, los problemas de transporte, los cambiantes códigos de construcción y el hecho de que la construcción sólo podía llevarse a cabo en invierno y principios de primavera, la "temporada baja" en la isla. Pasaron dos años antes de que empezara la construcción, y en los cuatro siguientes el equipo avanzó lentamente, edificio a edificio, fabricando e instalando 44 edificios formados por 455 módulos, cada uno de ellos completamente único.
HDC
El primer obstáculo para cualquier construcción en Nantucket es pasar la revisión del HDC. Los requisitos de diseño incluyen un determinado estilo de tejado a dos aguas con pendientes específicas, remates específicos, colores de puertas, materiales, tejados, etc. que hay que cumplir antes de que se expidan los permisos de construcción. Klamert llevaba los planos aprobados por el HDC a SBS y trabajaba con ellos para modular el diseño para la producción, y si se cambiaba algo, todo tenía que volver al HDC para que lo volviera a aprobar. Este proceso continuaba para cada edificio de la urbanización, tanto si se trataba de un edificio de apartamentos como de una vivienda unifamiliar.
Además, no podía haber dos edificios iguales en la isla, por lo que cada uno tenía que diseñarse individualmente. "Cada edificio era distinto", explica Klamert. "No podíamos tomar el mismo diseño y reutilizarlo una y otra vez. La comisión del distrito histórico no lo permitiría". Y la aprobación del diseño de cada edificio tardaba entre dos y seis meses.
Falta de experiencia
O'Hara y su equipo se enfrentaron a una ardua batalla: nadie del equipo de contratación tenía experiencia directa con la construcción modular. "Tuvimos que empezar de cero con ellos y explicarles qué era un sistema modular", explica O'Hara. "En un momento dado, enviamos el avión del jefe, reunimos a los fontaneros, electricistas y demás subcontratistas, los trajimos a nuestra fábrica y organizamos un seminario. Les enseñamos la fábrica y les explicamos lo que íbamos a hacer".
La realidad de trabajar en la isla es que la mayoría de la mano de obra vive en el continente. El trayecto en ferry a la isla dura 45 minutos y luego hay que recogerlos en el muelle, porque no suelen llevar vehículo. Luego tienen que salir de la obra a tiempo para coger el último ferry, porque si lo pierden, una habitación de hotel puede ser extremadamente cara. Los trabajadores suelen trabajar sólo seis horas antes de tener que volver a casa. "No se puede tomar impulso", dice O'Hara. "Se tarda una eternidad en construir algo".
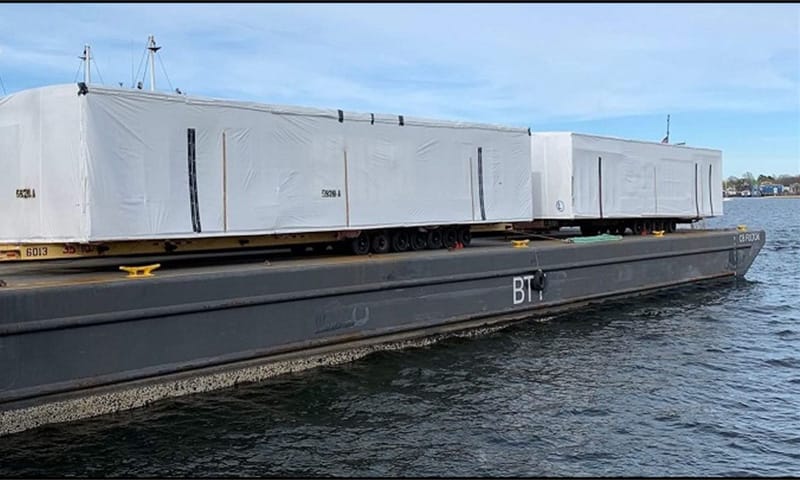
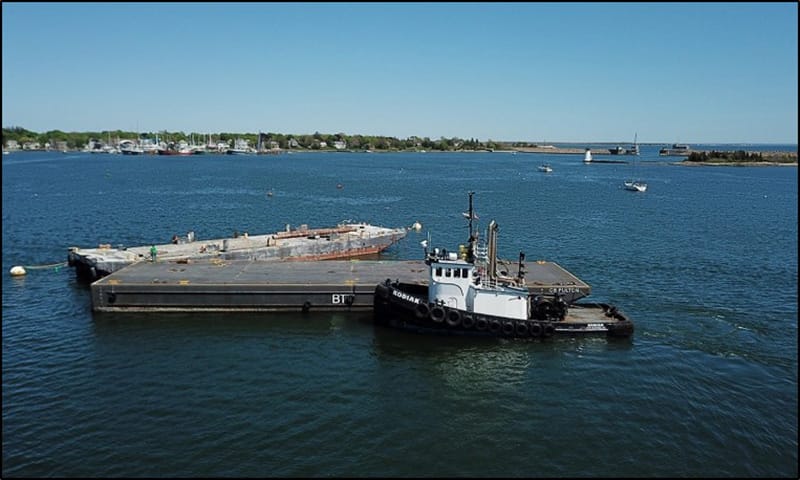
Cada módulo tuvo que hacer un viaje de 357 millas en camión hasta el muelle, y luego ser cargado en una barcaza para el viaje de 66 millas a través del océano hasta Nantucket.
Transporte
Los módulos fueron construidos por SBS en Scranton (Pensilvania). Después tuvieron que hacer un viaje de 357 millas en camión hasta el muelle, y luego ser cargados en una barcaza para el viaje de 66 millas a través del océano hasta Nantucket. El viaje fue más largo (Nantucket está a sólo 26 millas de la costa continental) porque el muelle donde se atracó la barcaza estaba más lejos.
Cada barcaza sólo podía contener cuatro módulos y sólo se podía botar una barcaza al día. El transportista de barcazas tenía un astillero que sólo podía albergar ocho módulos, así que SBS encontró un aparcamiento al otro lado de la carretera y calle arriba en el que podían instalar algunos módulos. O'Hara explica: "Los llevábamos hasta allí durante el día y los aparcábamos en la cabecera de la barcaza, e intentábamos cargar esa zona y el aparcamiento alternativo para que en el transcurso de, digamos, una semana, cinco días, pudieran pasar 20 módulos".
SBS descubrió que había un límite en el tamaño del módulo que podía manejar la barcaza. "La barcaza no podía soportar el límite de tamaño que podíamos construir. Lo aprendimos por las malas enviando módulos demasiado grandes, con los que consiguieron luchar, pero nos dijeron que no volviéramos a enviarlos. Dijimos: 'vale, no más módulos de 55 pies'", explica O'Hara. Los módulos variaban en anchura de 10' a 15'9" y en longitud de 27' a 55'. Hubo 53 variaciones en el tamaño de los 455 módulos necesarios para el proyecto.
Enviar los módulos en una barcaza también significaba que tenían que estar protegidos del duro clima oceánico durante los duros meses de invierno a lo largo de la costa este. "El agua pasaba por encima de la cubierta. Así que tuvimos mucho cuidado con la protección de los módulos. Tuvimos que desarrollar nuevas formas de protegerlos y encontrar nuevos materiales", explica O'Hara.
Cambios en el código
Otro reto fueron los cambiantes códigos energéticos a lo largo de los cuatro años que duró la construcción del proyecto. Massachusetts tiene códigos de eficiencia energética opcionales, llamados códigos de energía extensible, que se han adoptado en Nantucket. "Cuando empezamos, estábamos construyendo un producto que cumplía los códigos de Massachusetts", explica O'Hara. "Luego adoptaron el primer nivel de los códigos energéticos. Durante el proceso de construcción, el código cambió tres veces y cada una de ellas exigió enormes cambios de diseño."
Como ejemplo, O'Hara explicó que los primeros módulos enviados tenían conductos instalados en las vigas del suelo de cada planta del edificio de apartamentos. Luego instalaban un climatizador en cada unidad y enviaban la unidad exterior y la placa para que el contratista de HVAC la instalara in situ. En los últimos módulos que construyeron (cuatro años más tarde), el sistema HVAC se montó completamente in situ y estaba compuesto por un sistema dividido con unidades colgantes de pared, unidades de cabecera y unidades de cassette de techo. Como los juegos de líneas tenían que ser de tipo doméstico y los módulos eran seccionales, era muy poco lo que se podía hacer en una fábrica modular. Otros cambios consistieron en cambiar el aislamiento de fibra de vidrio por el de lana mineral, aumentar el aislamiento por soplado en techos y paredes, mejorar el cristal de las ventanas y sellar cada módulo lo suficiente como para superar las pruebas de soplado in situ.
Además, debido a la elevada humedad de la isla, la ventilación del semisótano era un requisito para estos edificios. "A veces hay que poner deshumidificadores y ventiladores en el semisótano con acceso al aire fresco exterior o por medios mecánicos", dijo Klamert.
Por si fuera poco, el equipo del proyecto tenía que hacer malabarismos con el diseño de módulos según una norma de código, mientras los contratistas instalaban módulos según otra norma de código diferente. Según O'Hara, "era un caos continuo, pero interesante. Nadie se enfadaba. No era ese tipo de cosas. La mayoría de la gente de la ciudad quería esta urbanización, así que nos dieron un respiro y nos ayudaron a hacer las cosas".
Lecciones aprendidas
O'Hara atribuye a este proyecto el impulso para el desarrollo y la expansión del departamento de ingeniería de SBS. "Añadimos gente, aprendimos cosas y ahora lo que hacemos es mejor. Ahora hacemos edificios de apartamentos pasivos y hemos aprendido todas esas técnicas trabajando en Nantucket. Todo lo que construimos, lo hacemos ahora de la misma manera, con la vista puesta en detener las fugas de aire y energía, lo que significa que has aumentado enormemente la eficiencia sin cambios adicionales en el diseño".
Cuando se le preguntó qué consejo daría a otros sobre la construcción modular en circunstancias similares, O'Hara respondió: "La construcción modular es una opción excelente para la construcción en islas, pero se requieren deberes y planificación. Iniciamos las conversaciones con nuestro cliente sobre este proyecto en febrero de 2017, pero no enviamos nuestros primeros módulos hasta abril de 2019. Lleva tiempo descubrir la mejor alternativa, evolucionar los mejores diseños y determinar los mejores materiales y técnicas. Y, lo más importante, formar el mejor equipo para llevar a cabo la tarea".
Sobre la autora: Dawn Killough es una escritora independiente especializada en construcción con más de 25 años de experiencia trabajando con empresas constructoras, subcontratistas y contratistas generales. Su obra publicada se puede encontrar en dkilloughwriter.com.
Más de Modular Advantage
Propuesta de Salario Compensatorio de Oregón: Una llamada de atención para la construcción modular
Si el proyecto de ley 2688A se convirtiera en ley, los proyectos de construcción aumentarían de precio, tendrían plazos de ejecución más largos y producirían muchos más residuos. El proyecto de ley también incentiva la adjudicación de contratos a empresas de fuera del estado que no reinvertirían sus ganancias en la economía local de Oregón.
Detrás del diseño de Bethany Senior Terraces, el primer proyecto modular de viviendas pasivas para personas mayores de Nueva York
A medida que aumenta el número de promotores que tratan de cumplir las nuevas normativas sobre eficiencia energética, el equipo de Murray Engineering ha establecido un nuevo récord. Con el proyecto Bethany Senior Terraces, Murray Engineering ha contribuido a desarrollar la primera estructura modular de Nueva York que cumple plenamente los principios de las casas pasivas, introduciendo una nueva era de eficiencia energética en la ciudad que nunca duerme.
Cómo utiliza LAMOD los módulos para abordar la ineficiencia, la sostenibilidad y el futuro de la construcción
Mientras promotores, diseñadores y contratistas tratan de entender las necesidades cambiantes del sector modular, nadie conoce tan bien las ventajas de la modularización como Mārcis Kreičmanis. Como cofundador y CBDO de LAMOD en Riga (Letonia), Mārcis se ha marcado como objetivo último acabar con las ineficiencias de la construcción tradicional.
De constructor de muebles a "arquitecto activista": El singular viaje de Stuart Emmons
A Stuart Emmons le fascinaban los edificios desde muy joven. Recuerda que construía ciudades de arena con su hermano durante los viajes a la costa de Jersey. Su padre le regaló su primera mesa de dibujo a los diez años. Hoy es un arquitecto experimentado que recibió su FAIA en junio de 2025. Su camino es, como mínimo, único.
Forja Artesanal Arquitectura + Diseño: Códigos, contratos y propiedad intelectual
Rommel Sulit, Director Fundador y Director de Prácticas Modulares de Forge Craft Architecture + Design, analiza las implicaciones de los códigos, los contratos y la propiedad intelectual en la construcción modular.
la construcción modular.
Eisa Lee, la arquitecta "bilingüe
Ahora, como fundadora de XL
Architecture and Modular Design en Ontario, Canadá, no sólo aplica su formación como arquitecta tradicional, sino también una visión holística del diseño modular. Es esta visión expansiva la que guía su trabajo para ser un verdadero socio que salva las distancias entre los arquitectos y las fábricas modulares a medida que colaboran en el proceso de diseño.
Ingeniería Tamarack Grove: Diseño para el sector modular
El papel de un ingeniero estructural es crucial para el éxito de un proyecto modular, desde el análisis inicial hasta la administración de la construcción. Tamarack Grove ofrece servicios de ingeniería estructural -análisis de proyectos, creación de planos, creación de diseños y administración de la construcción- para edificios comerciales, de fabricación, instalaciones, servicios públicos y modulares. El modular es sólo un sector del mercado al que la empresa presta sus servicios, pero es un sector cada vez más popular.
Un ingeniero domina el arte de escuchar a sus clientes
Desde que fundó Modular Structural Consultants, LLC. en 2014, Yurianto ha establecido una cartera estable de clientes de construcción modular y en contenedores, principalmente fabricantes. Sus servicios incluyen a menudo la realización de cálculos de ingeniería, la revisión de planos y la certificación de ingeniería.
Dentro de College Road: La ingeniería de los módulos de uno de los edificios modulares más altos del mundo
College Road es una innovadora urbanización modular en East Croydon, al sur de Londres, obra del promotor y contratista Tide, su empresa modular Vision Volumetric (VV), y diseñada por MJH Structural Engineers.
Diseño para el flujo: el poder ignorado del DfMA en la construcción modular
Conseguir un mayor rendimiento, menores costes y menos rediseños alineando el flujo de producción Lean con el diseño para fabricación y montaje.