La aldea del cañón de Yellowstone: un hito de la construcción modular diez años después
El parque nacional más antiguo del mundo necesitaba una gran renovación de alojamiento a finales de la década de 2000.
Antes de 2014, cualquiera de los 3,5 millones de visitantes anuales de Yellowstone que quisiera pasar una noche en la remota altitud de Canyon Village no tenía más remedio que alojarse en una cabaña anticuada tipo motel. Estas 200 cabañas, con un total de 410 habitaciones, se construyeron inicialmente en 1957 para hacer frente al aumento de visitantes (que entonces rondaban los 1,7 millones anuales) como parte del plan "Misión 66".
Unos 57 años después, Xanterra Travel Collection®, el principal concesionario del parque de Yellowstone, recibió el encargo de abordar el enigma de revitalizar el alojamiento en esta zona remota y elevada, propensa a condiciones climáticas extremas. De hecho, se embarcaron en uno de los mayores proyectos de construcción de alojamientos para el Servicio de Parques Nacionales, y lo hicieron en un tiempo récord con sistemas modulares.
En colaboración con Guerdon, LLC, una empresa de diseño y fabricación modular con sede en Boise (Idaho), Xanterra sustituyó las 410 habitaciones de Canyon Village en cinco alojamientos de varios pisos en sólo dos años. Gracias al diseño modular, Guerdon pudo conjugar la belleza rústica y natural de Yellowstone con los requisitos de resistencia y sostenibilidad necesarios para mantener esta propiedad única en su género.
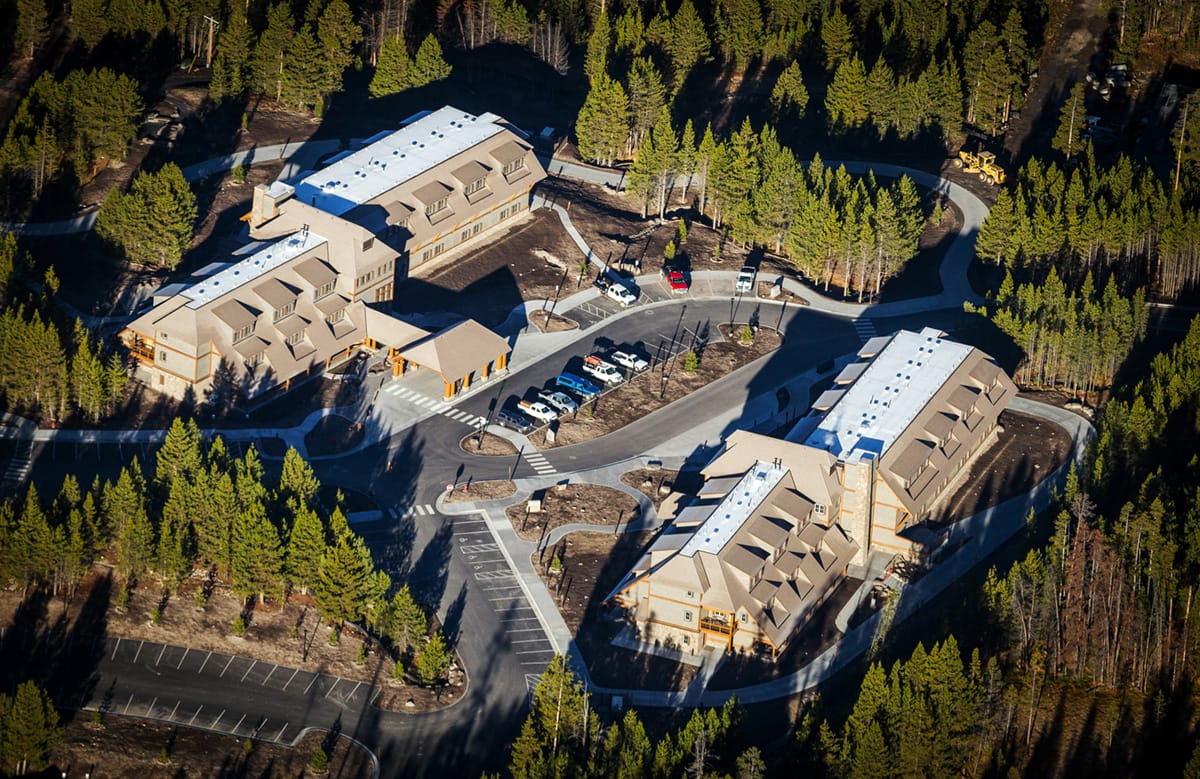
Vista aérea del Yellowstone Canyon Lodge, fabricado por Guerdon.
A punto para ganar en sostenibilidad gracias a las necesidades de elevación
Mike Keller, Vicepresidente/Director General de Xanterra, había visto la creciente necesidad de mejorar la oferta de alojamiento en Canyon Village durante su largo mandato en Yellowstone.
"Estaba previsto que [la Misión 66] durase cinco años, pero acabó durando cerca de 70", explicó. "Así que en Canyon Village se hizo patente la necesidad de construir servicios modernos y útiles para los visitantes. Canyon se encuentra a la mayor altitud de Yellowstone y suele tener algunas de las nevadas más importantes del parque".
Canyon Village, situada a menos de 2.000 metros sobre el nivel del mar, contaba inicialmente con edificios que parecían "auténticos vagones de carga, cabañas portátiles de techo plano que parecían fuera de lugar", explica Keller.
Por eso, cuando Xanterra concibió los alojamientos de sustitución, gran parte del diseño se centró en aplicar la resistencia y la sostenibilidad a estas estructuras. Cada edificio se creó con sistemas MEP y fachadas exteriores únicos:
- Minimice el impacto de la carga y la acumulación de nieve con tejados de pendiente elevada.
- Mantener la integridad estructural en relación con las fluctuaciones de temperatura debidas a condiciones meteorológicas extremas y a la actividad sísmica.
- Elimine las amenazas de agua congelada con tuberías inclinadas para extraer el exceso de agua de las tuberías principales y de seguridad antes del cierre invernal.
- Cumplir los requisitos de la certificación LEED.
- Facilitar al personal del parque los procesos anuales de vaciado invernal.
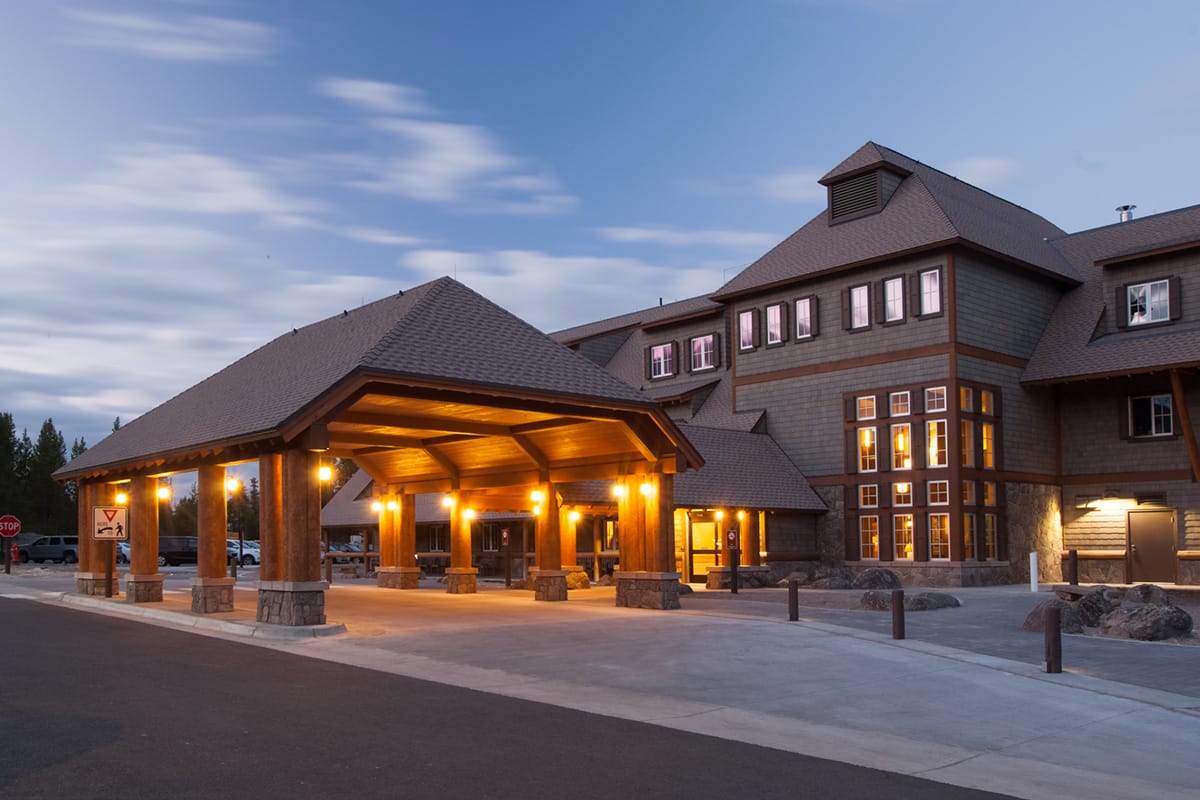
Del "tablero de dibujo" a la aplicación práctica
Como parte del Departamento de Desarrollo de Negocios de Guerdon, el Director de Diseño y Desarrollo de Productos Mitch Hovaldt se enfrentó a los desafíos creativos de cumplir con todos los requisitos de Xanterra para los lodges en Canyon Village. Los obstáculos se apilaron tan alto como el nivel de elevación de Canyon, como Hovaldt recuerda de 2013.
"Recibí una llamada de alguien que me dijo: 'Oye, mira, tenemos este proyecto, tenemos problemas de tiempo. Está en Yellowstone. ¿Qué podemos hacer para ponerlo en marcha?". Sobre el curso de un año, él revisó el plan de sitio para los cinco edificios para el departamento de ingeniería de Guerdon, creando la masa inicial, las disposiciones, y los procesos antes de trabajar en tándem con el equipo de diseño de fábrica.
El Gerente de Diseño de Guerdon Chad Hart, entonces un diseñador modular mayor, fue traído sobre el proyecto en 2014. Él se concentró en los detalles de producción de fábrica para asegurarse de que la fabricación podría emparejar las expectativas arquitectónicas, estructurales, y MEP dadas por Xanterra.
Cada módulo midió aproximadamente 13 pies 8 pulgadas de ancho, con una longitud típica de 54 pies, que estaba fácilmente dentro de la capacidad de fabricación de Guerdon. Juntos, los equipos de Hart y Keller estudiaron minuciosamente los planos, insertando tipos de material, tamaños de módulo, e incluso pequeños detalles como trabajo de azulejo.
"Fuimos a cada tipo de habitación y dibujamos todas las piezas que necesitaban", explica Hart. "Cada enchufe, cada lámpara, cada azulejo, todo lo que habíamos diseñado en nuestro modelo Revit, todo calculado para que pudiéramos ayudar a nuestro grupo de producción a construirlo de forma más eficiente".
Además de los acabados internos, los diseños de la cubierta obligaron a Guerdon a replantearse las prácticas de fabricación para satisfacer las exigencias medioambientales de Yellowstone.
Cubiertas inclinadas y retos de fabricación para el desagüe invernal
Según Hovaldt, los tipos de unidades del nivel superior exigían una reflexión compleja y soluciones creativas. El diseño inicial presentó un "techo de estilo de capa," con ángulos agudos típicamente no encontrados en diseños de cubo modulares, desafiando al equipo de diseño de Guerdon para asegurar que todo alineó correctamente.
Además, Xanterra estaba "comprando paquetes de cerchas que iban a sobreconstruir encima de los módulos que estábamos entregando, teníamos que tener un paquete de diseño altamente coordinado con ese piso de nivel superior", dijo Hovaldt. "Teníamos buhardillas que sobresalían de eso, y eran buhardillas de ventanas dentro de las suites también".
"Dedicamos mucho tiempo a desarrollar las unidades de nivel superior para asegurarnos de que todos los ensamblajes de paredes y techos eran correctos", dijo. "Aunque nuestra fábrica tiene procesos establecidos para construir paredes y techos, añadimos un componente extra para acomodar la pared en ángulo necesaria para el sistema de techo. Esto añadió un poco más de complejidad a las operaciones de nuestra planta, pero era necesario para lograr el diseño."
Hovaldt y su equipo también instalaron un componente de barrera de vapor que también sirvió para reforzar la integridad estructural ante dichas condiciones climáticas extremas, como fuertes cargas de nieve.
"También tuvimos que colocar un revestimiento de polietileno detrás de los paneles de yeso como barrera de vapor, según las especificaciones. Eso estaba un poco fuera de nuestro ámbito con el que nos sentíamos cómodos en ese momento, pero nos las arreglamos para que todo eso funcionara."
Además del trabajo de fabricación, las tuberías inclinadas y los elementos de calor radiante requirieron que Hart y su equipo diseñaran techos y pasillos con amplios espacios para ayudar a Canyon Village en sus esfuerzos anuales de acondicionamiento para el invierno.
Según Dylan Hoffman, Director de Sostenibilidad de Xanterra, las tuberías sutilmente inclinadas y las válvulas estratégicamente situadas, que utilizan la gravedad para evacuar el agua durante el invernaje anual, fueron funciones de diseño cruciales.
"Cuanto menos tiempo tengamos que dedicar a la preparación individual para el invierno de cada uno de estos edificios, más tiempo podremos dedicar a otros aspectos cruciales en la preparación de estas instalaciones para un invierno largo y frío", dijo. "Era un objetivo importante para nosotros y algo que ha funcionado bien".
Incluso con todas estas anomalías de diseño en juego, el principal reto que estaba en la mente de todos era: ¿Con qué rapidez se podían transportar e instalar con grúa estos módulos?
Transportar módulos en temporada baja evitó la presión del tráfico
Una parte de las inusuales restricciones de construcción de Canyon Village tuvo que ver con una simple variable: el tiempo. Los meses más activos del año en Yellowstone son los de verano, de mayo a octubre. Canyon Village se encuentra a una hora al noreste de Old Faithful y sólo es accesible por dos carreteras principales. Después de octubre, las dos carreteras principales permanecen cerradas durante el invierno.
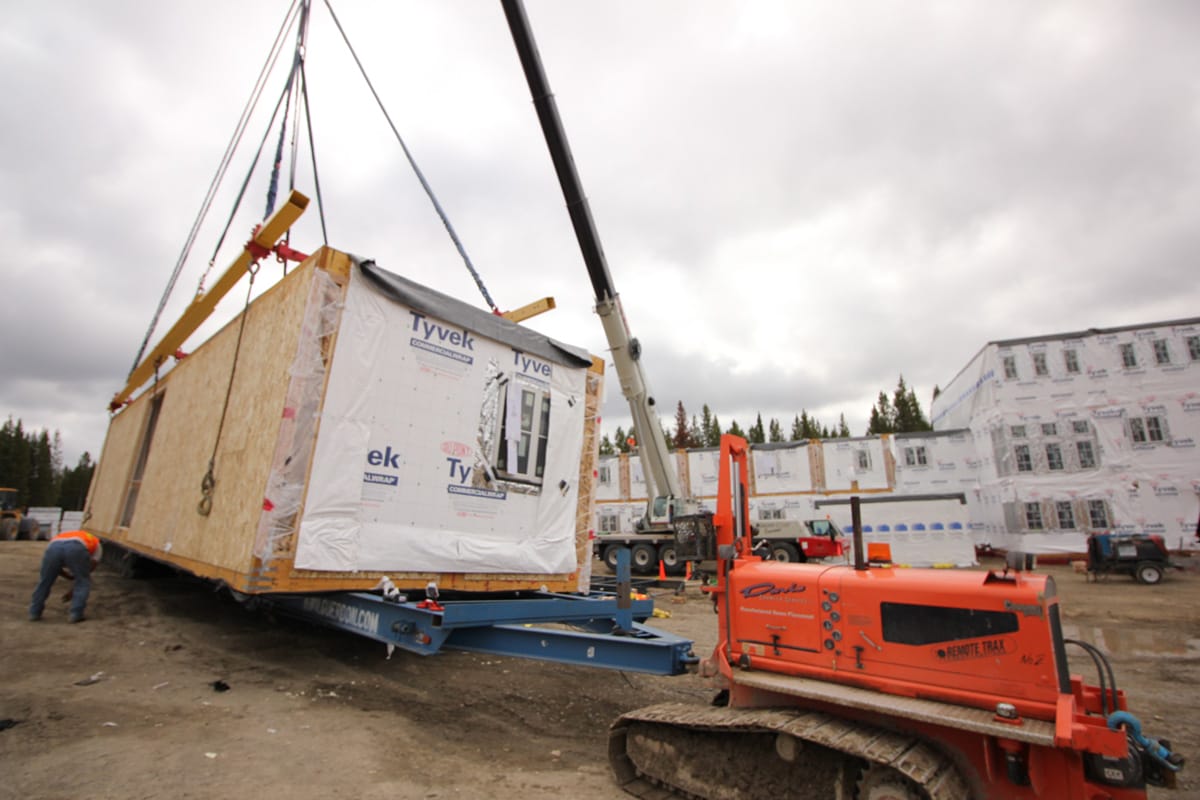
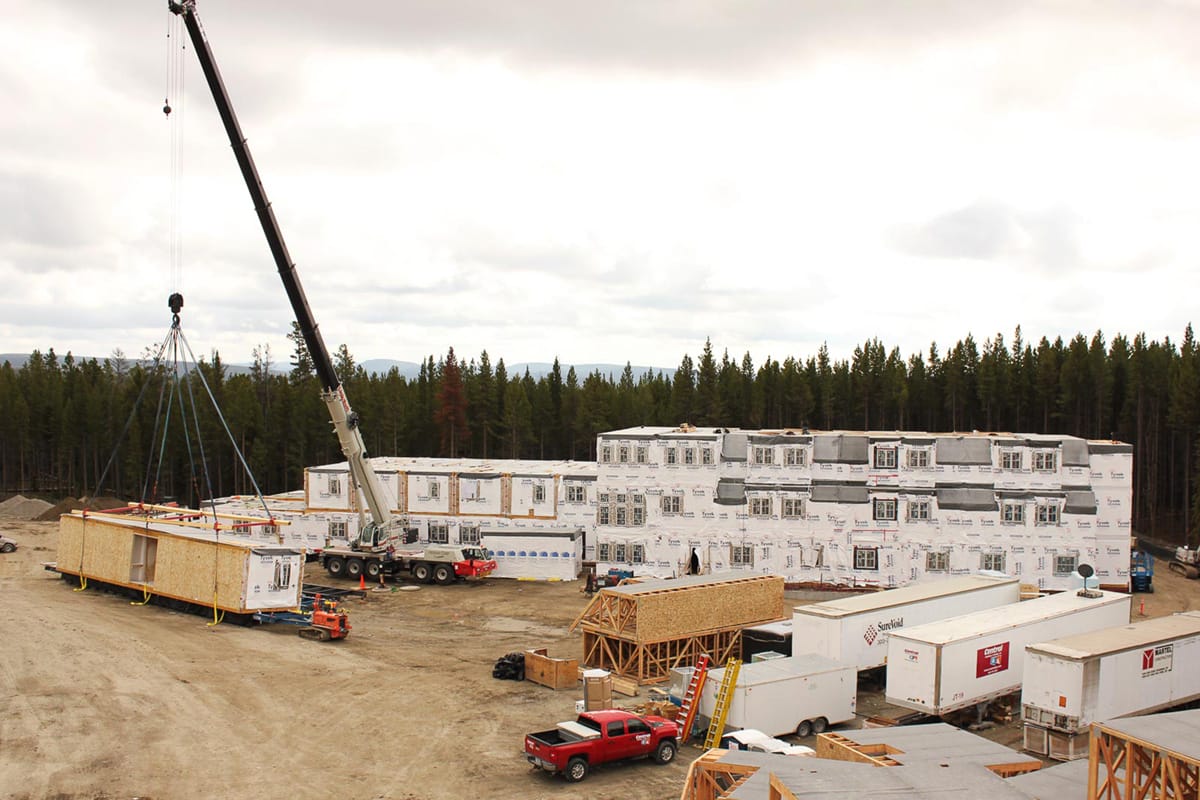
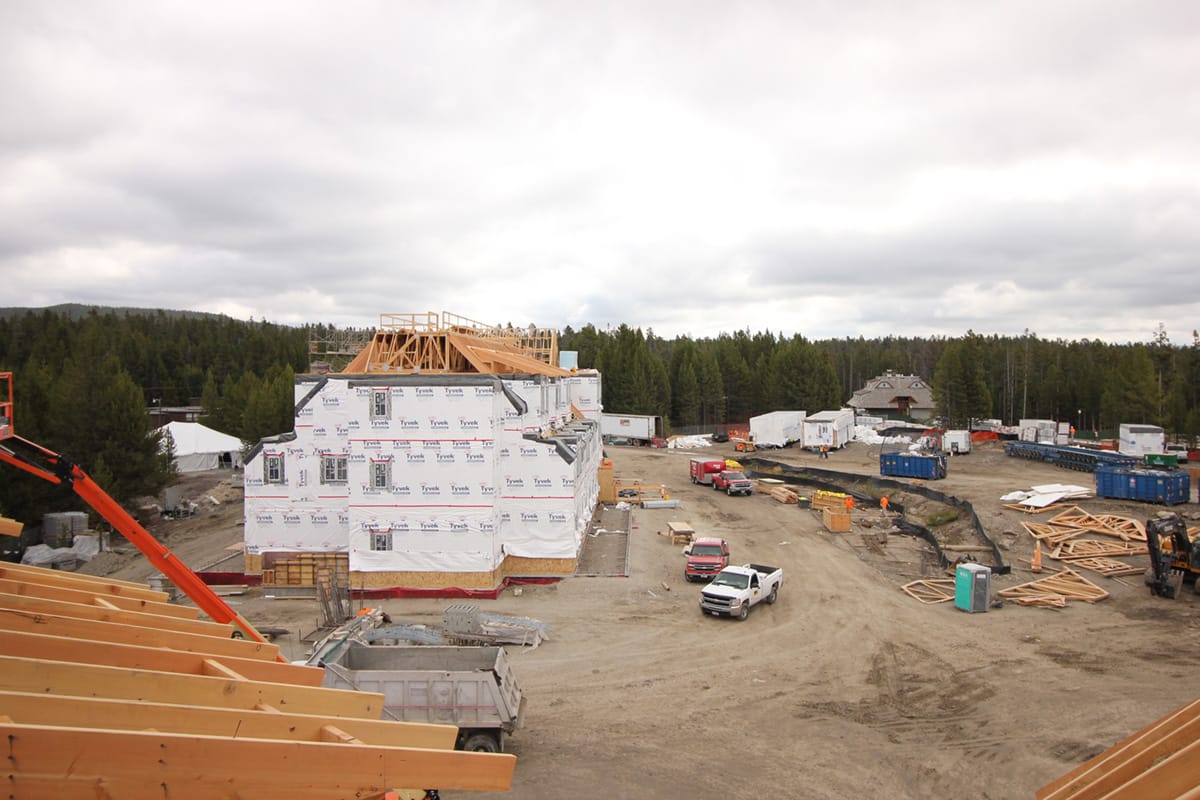
Guerdon y el equipo de decorados modulares se enfrentaron a numerosos retos debido a las condiciones meteorológicas, los visitantes del parque y la remota ubicación del lugar.
Con un periodo de construcción tan corto, lo más lógico para Xanterra era optar por los módulos. La gran afluencia de visitantes a Yellowstone también exigió una programación del transporte un tanto extraña, ya que el tráfico procedente de la entrada de West Yellowstone determinaba las horas a las que los camiones podían descargar los módulos.
En julio de 2014, Guerdon empezó a enviar los primeros módulos a Yellowstone, trasladándolos en dos etapas: de Boise a la entrada de West Yellowstone y de West Yellowstone a Canyon Village.
Sin embargo, a menudo los transportistas llegaban fuera del horario del parque y durante las temporadas bajas, dijo Hoffman. El transporte por módulos se destinaba a esas temporadas bajas antes de que el parque abriera y cerrara en serio. Antes de que el parque abriera para la temporada principal, las máquinas quitanieves entraban desde el 25 de marzo hasta el 5 de abril aproximadamente para limpiar la nieve. En otoño, las carreteras se mantenían desde el 1 de noviembre hasta el día de Acción de Gracias después del cierre. En ambos periodos, los camiones podían entrar y descargar módulos sin tener que lidiar con el tráfico de visitantes.
Fue necesario un poco de malabarismo administrativo y logístico para hacer posible la doble puesta en escena, ya que se formaron colas de camiones gigantes para entrar por la entrada oeste y, finalmente, se estacionaron en el parque.
"Se trataba de minimizar el impacto tanto en los empleados como en los desplazamientos por el parque en general", explicó Hoffman.
Mike Keller también se hizo eco de las dificultades logísticas, señalando que "mientras estábamos abiertos en algunas de esas primeras y últimas semanas, se hacían recorridos, pero a altas horas de la noche, temprano por la mañana, cuando el tráfico era mínimo o no había tráfico en la carretera. Había vehículos con banderas, coches piloto, todo lo que se puede esperar en carreteras estrechas de montaña", explicó.
Excavación de túneles de nieve, grúas desplazando módulos in situ
Como el sistema de cubierta también llevó a Guerdon a sus límites creativos, la instalación de todos los módulos in situ con estos techos de ángulos pronunciados proporcionó un aspecto de trabajo inusual en la obra. Además, las inminentes inclemencias del tiempo dificultaron la instalación.
El equipo de diseño de Guerdon tenía experiencia con condiciones extremas de frío, pero el cierre repentino y la caída de la construcción reforzaron el valor de los módulos herméticos y el edificio estaba completamente seco antes de que llegara la nieve, según Mitch. En el otoño de 2014, tres edificios habían sido enviados y grúa instalada, con todos ellos totalmente secado en antes de cualquier caída de nieve.
Las instalaciones internas y los trabajos de construcción continuaron durante el invierno.
En un momento dado, "hubo que cavar túneles a través de la nieve para entrar en los edificios porque la nieve era muy profunda" para los equipos que trabajaban en el interior del edificio con grúa, dijo Hovaldt.
Una vez llegada la primavera de 2015, la construcción continuó y se enviaron los dos últimos edificios y se instaló la grúa.
Cómo encontrar las molduras de pino adecuadas para la certificación LEED
Otra pieza importante del rompecabezas de la producción estaba relacionada con la certificación LEED. El contrato de Xanterra con el Servicio de Parques Nacionales estipulaba el uso de materiales reciclables específicos y requisitos de contratación local. Según Hoffman, Xanterra también aspiraba a la certificación LEED Plata con el proyecto Canyon Village. Por ejemplo, la elección de un sistema modular ayudó a conseguir la certificación LEED al desviar significativamente cerca del 85% de los residuos de la construcción.
"Con la versión LEED que utilizábamos en aquel momento, la de 2009, había créditos por materiales regionales", explica. "Todo lo que se obtuviera en un radio de 800 km podía obtener créditos por ello o por utilizar madera certificada. Así, si utilizas madera certificada FSC o SFI en todo el proceso, puedes obtener puntos en función del porcentaje que utilices. Lo mismo ocurre con los materiales con contenido reciclado".
Guerdon trabajó con proveedores para obtener materiales como madera de pino azul escarabajo para los acabados, encimeras de vidrio reciclado, pinturas de bajo contenido en COV y alfombras de materiales reciclados. El reto, según Hovaldt, fue tratar de encontrarlos dentro del radio designado del emplazamiento del proyecto.
El trabajo que hay detrás de la obtención de la certificación LEED se encuentra en los detalles cotidianos de los módulos, como la iluminación LED, los cabezales de ducha de bajo caudal, las cisternas de inodoro de un galón por minuto, los interruptores inteligentes, las ventanas de alto rendimiento y mucho más. Todos estos pequeños detalles ayudaron a Canyon Village a gestionar los recursos de forma más eficaz, dijo Dylan.
La planificación previa dio sus frutos, ya que cuatro de los edificios de Canyon Village tienen la certificación LEED Oro, y el quinto obtuvo la LEED Plata.
Las estadísticas del éxito de Canyon Village
Tras la apertura de los albergues en 2016, el número de visitantes anuales que acuden a Yellowstone aumentó de 3,5 a cerca de 4,5 millones, y las cifras siguen aumentando. La construcción de los alojamientos de Canyon Village sigue siendo a día de hoy el mayor proyecto de construcción sostenible de la historia del Servicio de Parques Nacionales.
"Es uno de los primeros proyectos modulares que se llevan a cabo en un bosque nacional en todo el país", dijo Hart. "Es algo muy importante".
Los cinco edificios siguen funcionando admirablemente, sin apenas efectos meteorológicos ni reparaciones necesarias para ajustar el funcionamiento cotidiano.
"Estos edificios son duraderos. Han durado, han resistido bien", dijo Keller. "Han resistido los elementos y los retos de nuestra estacionalidad aquí en el parque, y este proyecto estaba muy bien construido, y sigue mostrándose y beneficiándose de esa manera".
El proyecto Canyon Village también se destaca como uno de los cinco mejores proyectos para Chad Hart y Mitch Horvaldt en Guerdon. Mike Keller de Xanterra y Dylan Hoffman también miran hacia atrás con cariño a la construcción de Canyon Village como uno de sus tres primeros.
Sobre la autora: Karen P. Rivera es redactora y editora independiente apasionada por la narrativa. Ha sido reportera en las Naciones Unidas y tiene experiencia en noticias internacionales de última hora, capital riesgo, tecnología sanitaria emergente y la industria de los videojuegos.
Más de Modular Advantage
La vivienda como infraestructura esencial
La crisis de la vivienda no es nada nuevo. En todo el mundo, los gobiernos federales, estatales y municipales de todos los tamaños se esfuerzan por proporcionar viviendas más asequibles, rápidamente, a quienes las necesitan. En Canadá, Paul Halucha, Viceministro de Vivienda, Infraestructuras y Comunidades (HICC), afirma que el papel del gobierno federal en materia de vivienda ha pasado de la financiación a la configuración activa de los resultados.
Construir el futuro
Ante la crisis nacional de la vivienda, Inglaterra se encuentra en un punto de inflexión crítico en el que la innovación, la escala y las asociaciones público-privadas deben converger para satisfacer una necesidad urgente: más viviendas, y rápido. Homes England está ayudando a remodelar el mercado de la vivienda apoyando activamente a MMC mediante una combinación estratégica de promoción de suelo, financiación y subvenciones.
POJI y MOKO industrializan la construcción modular mediante sistemas de ingeniería automatizados
Trabajando con Scandinavian Industrialized Building System (SIBS), POJI y MOKO ayudaron a realizar un concepto de ciudad modular situada en el municipio de Järfälla de Estocolmo (Suecia), con 350 apartamentos, zonas comunes, restaurantes, pequeñas tiendas y un centro preescolar en una agradable mezcla con arquitectura experiencial y vegetación.
La misión de Boutique Modern de hacer asequibles y eficientes las primeras viviendas en el Reino Unido.
La empresa, con sede en el Reino Unido, lleva 12 años fabricando casas tanto para clientes privados como para la administración local, y gran parte de su negocio procede de la vivienda social y "asequible". Boutique Modern, que trabaja en una fábrica de 32.000 metros cuadrados en Newhaven (Sussex), está cambiando décadas de ideas sobre la construcción de casas, todo ello mediante el uso de módulos.
BoulderMOD: producción de viviendas modulares asequibles y formación de la mano de obra del futuro
Colorado ha sufrido un doble golpe: la disminución del número de trabajadores cualificados de la construcción y una mayor necesidad de viviendas asequibles. BoulderMOD, una asociación entre la ciudad de Boulder, Flatirons Habitat for Humanity y el distrito escolar del valle de Boulder, está abordando ambos problemas y ayudando a otros a hacer lo mismo.
Guerdon: en busca del "Santo Grial" de la construcción modular
Guerdon, un fabricante modular en Boise, Idaho, recientemente ganó lo que Laurence (Lad) Dawson, CEO y Socio Gerente, describe como el 'santo grial' para un fabricante modular. El RFP llama para una tubería de seis proyectos, totalizando aproximadamente 570
unidades.
La situación del sector modular en 2025: Afrontar la realidad
La realidad crítica y urgente es que la industria modular necesita abrir las puertas a la colaboración entre todos los sectores. Cuanto antes nos enfrentemos a estos retos, antes podremos dar la bienvenida a una nueva realidad en la que el sistema modular sea la forma dominante de suministrar viviendas de mejor rendimiento y calidad, y todo ello a un coste menor.
Viviendas multifamiliares modulares como solución escalable a la crisis de la vivienda
GreenStaxx ofrece una solución real y escalable a través de su biblioteca estandarizada de diseños multifamiliares modulares y su innovador modelo de tres pisos. Juntas, estas ofertas responden a las dos mayores necesidades del sector: eficiencia y adaptabilidad. Al centrarse en la calidad, la repetibilidad y la colaboración, GreenStaxx está contribuyendo a que la construcción modular pase de ser un nicho a convertirse en una corriente dominante y ofrece una vía práctica para resolver la escasez de viviendas.
Sellado para el éxito: El papel de la impermeabilización en la construcción modular
El agua es una de las mayores amenazas para cualquier edificio, causando daños estructurales, crecimiento de moho y costosas reparaciones si no se gestiona adecuadamente. La impermeabilización es la primera línea de defensa, ya que garantiza la durabilidad y el rendimiento a largo plazo. A medida que evolucionan los métodos de construcción, también lo hacen las soluciones de impermeabilización, pasando de los revestimientos tradicionales a sistemas avanzados listos para usar en fábrica.
Del volumen a la velocidad: Ampliar proyectos multifamiliares sin perder el control
Cuando los proyectos crecen demasiado rápido sin los sistemas adecuados, las fábricas tienen problemas. No cumplen los plazos, los equipos se agotan y la calidad disminuye. En lugar de un progreso constante, se desata el caos. Las cosas se ralentizan, incluso cuando pasan más unidades. Esto se debe a que no basta con fabricar más, también hay que fabricar de forma más inteligente. Eso significa pasar del volumen a la velocidad.